- Szczegóły
- Opublikowano: 14 marzec 2015
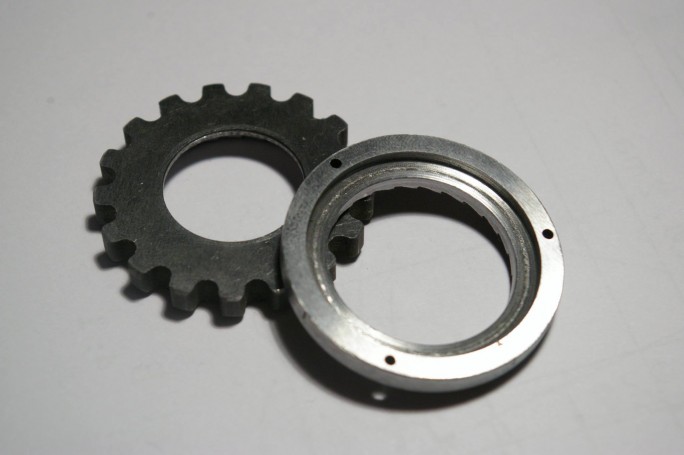
Głównym celem, jaki przyświeca nam przy opracowywaniu koncepcji pojazdu HYDROS jest minimalizacja strat energii. Wymaga to przemyślenia konstrukcji każdego podzespołu, zarówno w aspekcie pojedynczego elementu jak i całego pojazdu. Ze względu na konkretne przeznaczenie tej ekologicznej platformy jakim są zawody Shell Eco Marathon, konstruktor musi dostosować rozwiązania techniczne nie tylko do rygorystycznego regulaminu, lecz także do strategii przyjętej przez zespół na czas konkursowego przejazdu.
Już na etapie opracowywania pierwszych, luźnych koncepcji nasz zespół musiał zadecydować, czy bardziej wydajne jest rozpędzenie pojazdu, wyłączenie napędu i ponowne rozpędzenie gdy wytraci już prędkość, czy utrzymywanie w miarę stałej prędkości jazdy.
Po przeanalizowaniu zagadnienia, postanowiliśmy że będziemy trzymać się pierwszej strategii. Rozpędzony pojazd miałby toczyć się, wytracając swój pęd w jak najdłuższym czasie. Bez zastosowania elementu odłączającego napęd od koła jezdnego, podczas jazdy z wyłączonym silnikiem znaczne straty powodowałaby obracająca się przekładnia wraz z wirnikiem silnika. Naturalnie należało zastosować sprzęgło. Naszym głównym założeniem było, by sprzęgło przekazywało 100% momentu obrotowego gdy jest załączone, oraz brak strat podczas jazdy ‘na luzie’. Przewertowaliśmy dostępną nam literaturę i Internet w poszukiwaniu odpowiedniego typu sprzęgła, jednak żaden komercyjny produkt nie spełniał naszych oczekiwań – także ze względu na cenę i masę. Postanowiliśmy opracować własną konstrukcję.
Od początku inspirowaliśmy się mechanizmami stosowanymi w kolarstwie, natomiast ciekawą koncepcję podsunął nam mechanik z zaprzyjaźnionego sklepu rowerowego, którą postanowiliśmy dalej rozwijać. Nieoceniona okazała się także wiedza lokalnego producenta części rowerowych. Dzięki temu dość szybko powstał pierwszy projekt, który następnie należało zoptymalizować pod kątem zmniejszenia masy i zachowania odpowiedniej wytrzymałości. W tym celu wykorzystaliśmy oprogramowanie CAD i MES. Szybkie prototypowanie metodą stereolitografii umożliwiło nam sprawdzenie dokładności zazębienia. Po zatwierdzeniu ostatecznego projektu przez zespół zleciliśmy wykonanie rzeczywistych elementów. Pierścienie wykonane zostały ze stali technologią frezowania, toczenia, elektrodrążenia i szlifowania. Poddane zostały także obróbce cieplnej w celu polepszenia właściwości mechanicznych materiału. Istotą działania sprzęgła są kołki sterujące umieszczone w nieobracającej się osi poruszające pierścieniem umieszczonym w kole przekładni, współpracującym z nieprzesuwnym pierścieniem zamontowanym na sztywno w korpusie piasty. Rozłączenie i załączenie sprzęgła następuje automatycznie wraz z przerwaniem lub wznowieniem pracy silnika, dzięki czemu cała operacja odbywa się bez udziału kierowcy. Również natychmiastowe wysprzęglenie dodatkowo minimalizuje straty energii.
Mamy nadzieję, że już niebawem także pozostałe elementy będą gotowe tak, byśmy mogli wreszcie poskładać poszczególne podzespoły i przetestować działanie sprzęgła w praktyce.
Autor: Rafał Saj